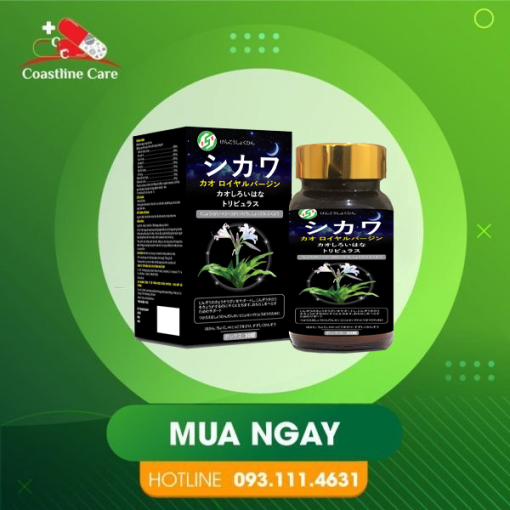
Ultimately, Ishikawa Diagrams are a great tool for fixing organization complications and determining the foundation brings about of complications. Groups can effectively use Ishikawa Diagrams to search out detailed answers by pursuing finest procedures such as clearly defining the issue, involving a various workforce, brainstorming probable results in, and prioritising root results in.
Ishikawa diagram, also referred to as the Fishbone diagram, is usually a Resource accustomed to recognize challenges in a method. It displays how leads to and outcomes are linked and can help evaluate what is going Incorrect with systems, procedures, and items. The name arises from Japanese engineer Kaoru Ishikawa who produced the tactic in the sixties.
Analizar el sector de atención al cliente de una empresa. Se pueden analizar los factores que intervienen en este sector para adaptarlo a las necesidades de los clientes.
Most international guests usually are not aware about the beauty of Noto Peninsula in Ishikawa prefecture. From the beaten route, it offers a top quality holiday vacation for the entire spouse and children. If taking a tour by bus or..
Draw a horizontal line extending from the condition assertion to the left. This is the fish’s backbone and serves like a Basis for that possible will cause.
Building an Ishikawa Diagram is an easy approach that begins with pinpointing the condition and breaking it down into its part pieces. Listed here’s a stage-by-move tutorial for generating an Ishikawa Diagram:
Discover leads to that are not impacting the impact as well as establish causes that have to have further investigation.
Making the diagram includes collaboration, significant thinking, and also a methodical method of detect and evaluate all achievable causes. The next can be a phase-by-step guide that can assist you produce an Ishikawa diagram.
One more limitation is the lack of apparent remedies or indications of the program of motion. An Ishikawa diagram helps to establish possible triggers, but determining the best strategies to fix the trouble generally requires further Assessment and evaluation. There exists also a hazard that placing an excessive amount nha thuoc tay of emphasis on figuring out brings about in just internal processes and techniques may possibly divert notice from external aspects that will have equally as Substantially impact on the problem.
A producing plant was suffering from high-quality Command troubles with their items. The issue was discovered making use of an Ishikawa Diagram, which helped the staff to recognize the possible results in of the trouble.
Increase your Lean Six Sigma tasks with our no cost templates. They are designed to make implementation and management less complicated, helping you accomplish nha thuoc tay much better effects.
Beneath is surely an example of a fishbone diagram for a producing enterprise. During this circumstance, the corporate employs the 6Ms to higher comprehend the causes of the problem, which happens to be that a Element of nha thuoc tay the product or service is in the incorrect dimension.
Following the brainstorming session, assess the diagram to ascertain the probably root leads to of the trouble.
Stage six: Determine the root reason behind the condition by evaluating likely will cause and sub-leads to. The basis bring about is the underlying situation which is producing the issue getting investigated.